Thoughts from the Alliance: the notion of “Cascade Recycling“
Overview
Recycling is most often broadly grouped into either Mechanical Recycling or Chemical Recycling. Find out how these approaches can be used in sequence, keeping materials in circulation at the highest level of quality, economic, and environmental value as long as possible.
By Martyn Tickner, Chief Advisor of Project Development, Alliance to End Plastic Waste
In a previous article, we likened the roadmap of Unmanaged Waste to Circularity to a jigsaw puzzle; there are many different contributing pieces to the solution and they all have to be fitted together. You need an idea of the big picture in order to know how to place the individual pieces of the puzzle.
In our case, the big picture has many pieces—Reduce unnecessary consumption; Reuse where we can; Substitute materials with more sustainable options; put in place basic waste management systems with Collection & Disposal, Sorting, and Recycling; use Renewable Feedstocks where it makes sense; source Economic Interventions to fund solutions; adapt Consumer Behaviour to create good habits; and Clean-up to address the legacy. All these elements are part of the puzzle of building a successful circular economy.
Previously we talked about high-tech solutions for sorting of used plastic—the centre of our puzzle—choosing to focus on high-income, well-regulated, and strongly committed regions. From there we can explore different areas piece by piece, leading to a vision of the future—and the journey to get there.
Next up is Recycling.
Within the many different technologies that exist, Recycling is most often broadly grouped into either Mechanical Recycling or Chemical Recycling. However, rather than diving into technologies, let’s keep in mind the bigger picture and look at three different levels of recycling output quality.
Closed Loop Recycling
Technically, a closed loop is a supply chain concept, the return or take-back of an object to Reuse or Recycle back into the same application. However, adopting a slightly broader context, we can consider closed loop to mean recycling back to a similar quality as the original material—a product fit-for-purpose to use again in the original or in a similarly demanding application.
Closed loop is our preferred option in respect of economic and environmental value.
However, the quantity of feedstock available for closed loop recycling is usually limited by lack of quality of segregation, collection, and sorting of used plastic. Also, national regulations may further restrict the ability to use recyclate in highly regulated markets such as food applications.
The best-known example of closed loop plastic recycling is PET bottles, returned to make new PET bottles. Bottles are easily recognised and collected separately from other plastics; the technology exists to wash, flake and recycle; the economics (generally) work, with recycled PET (r-PET) in high demand. And where r-PET does not meet the stringent quality standards for food grade, it still has other useful (down-cycling) opportunities.
Open Loop Recycling
Often the quality of the plastic available is compromised due to the presence of different types of plastics; mixed grades of the same plastic; and/or organic contamination. In addition, some plastics degrade after each time around the recycling loop and after 3 to 10 cycles, are no longer good for further use.
Where quality is compromised, the used plastic can be mechanically recycled into a lower quality application—also known as ‘downcycled’—typically into products such as garden furniture, paint pails, buckets, and basic building and construction materials. In our PET example, this would be into textiles, or food trays.
Open Loop recycling may not be as good a solution as Closed Loop, but it is still a good alternative—offering both economic value and a reduction in carbon footprint versus making new virgin plastic and/or disposal to landfill or waste-to-energy. Furthermore, such applications often have a long life cycle, meaning the carbon that is used to make the product is sequestered (locked up rather than released into the atmosphere) for a period of time.
The scale of Open Loop recycling is, like Closed Loop, still constrained by available feedstock quantity and quality. Even if feedstock were available, there is also a challenge to find markets that are big enough to absorb all the production.
Upcycling
This is where the output of the recycling process has a higher quality than the plastic feedstock, or input. There are multiple different technologies which are being developed—for example enzymatic conversion processes, or advanced mechanical recycling processes such as solvolysis. Most typical however is chemical recycling, where a plastic product is broken down or depolymerised back to raw materials.
The advantage of chemical recycling is that it enables production of plastic which is of fully equivalent quality to the original virgin plastic, and overcomes any regulatory constraints on the use of the recyclate in demanding applications such as food or medical use. However, chemical recycling technologies will typically have a higher carbon impact than Closed Loop or Open Loop recycling, and a higher operating cost (hence lower value capture) than Closed Loop recycling.
Working together in tandem: Cascade Recycling
So from the above, it should be clear that no one solution in itself is optimal. Time will determine what percentage of our recycling comes from which approach, but certainly all three will be deployed. The ideal approach is to use these approaches in sequence, known as Cascade Recycling, keeping materials in circulation at the highest level of quality, economic, and environmental value as long as possible.
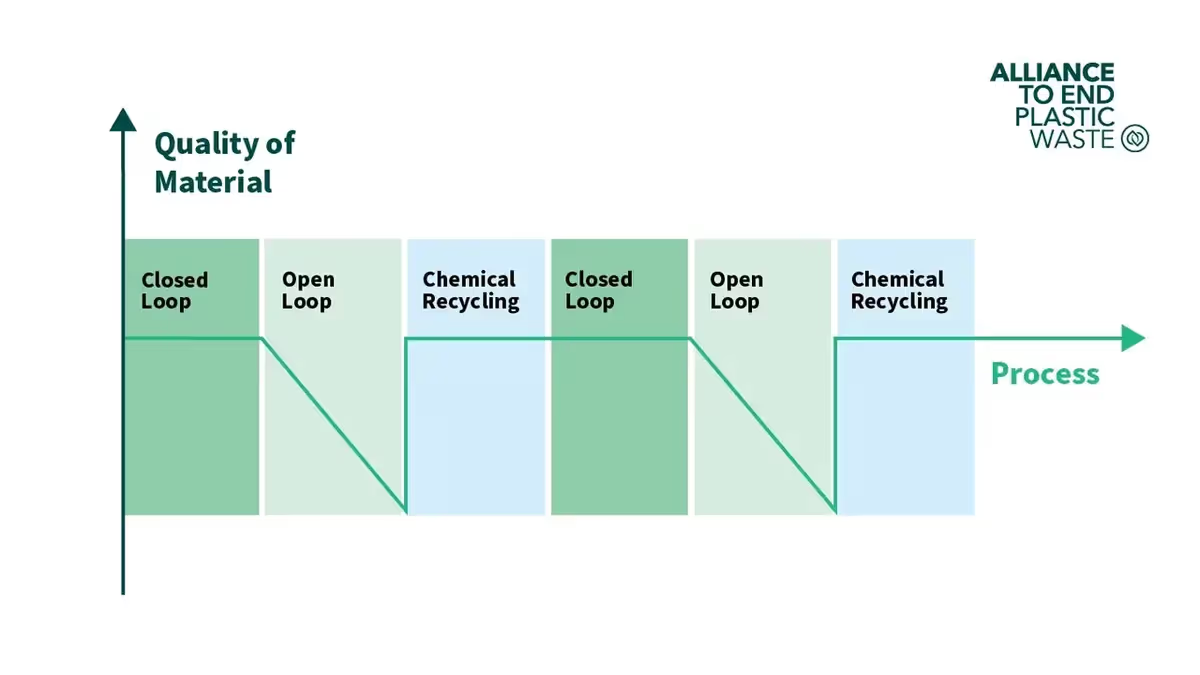
Firstly, use Closed Loop Recycling as much as possible—limited by the availability of high-quality feedstock.
Then use Open Loop Recycling, to the extent market opportunities make economic sense.
Then use Chemical Recycling to lift what cannot be mechanically recycled back to the highest level of quality, identical to the original virgin plastic.
And repeat—over and over again. This is circularity in action.
The journey towards circularity
The solutions to do this exist, or are being developed at a remarkable pace. However, with less than 10% of the world’s plastic waste being recycled today, we need huge investments in recycling capacities to create this cascade of Closed Loop, Open Loop, and Chemical Recycling.
This is a very important area of focus for the Alliance: to support demonstration of viable technical solutions and business models; and to understand what is needed to drive the mobilisation of capital and large-scale adoption of the technical solutions to rapidly expand the world’s recycling capacity.
Still, there are many pieces of the jigsaw puzzle to be found.
Which players in the value chain will take the lead in consolidating today’s highly fragmented industry? How do we consolidate feedstock streams to achieve critical scale? Who will invest in new, state-of-the-art sorting and recycling facilities and drive the necessary quality approaches? How long will it take the industry to convert complex multi-material plastic films to structures which are more recyclable—and build the facilities to recycle them?
Perhaps most challenging of all: what economic interventions are required to enable the recycling industry to compete with virgin plastic?
Follow our discussion as we tackle those questions next, building out the puzzle piece by piece.
Stay in the loop
Subscribe to our newsletter for the latest news and updates from the Alliance