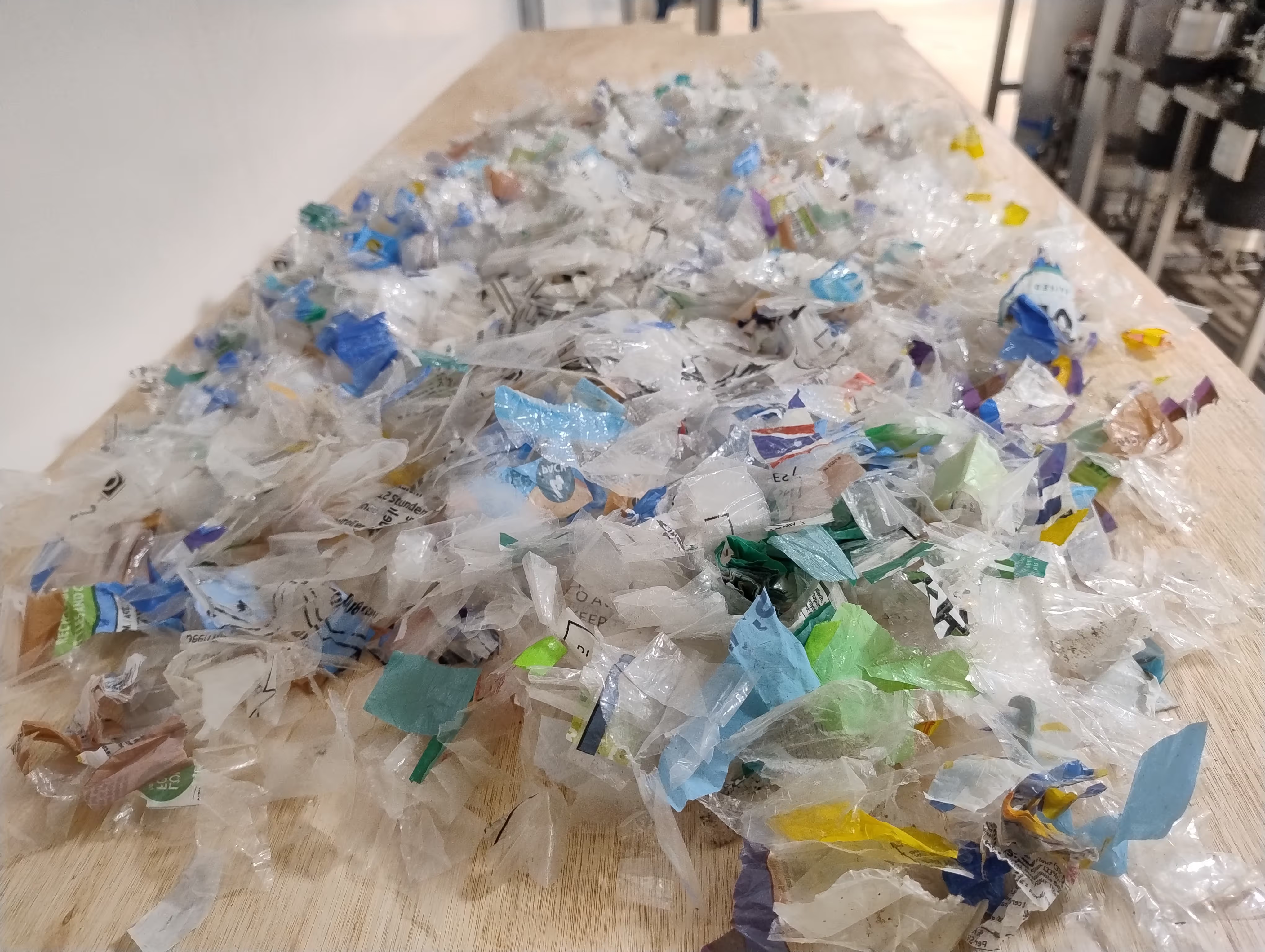
The super-critical COtooCLEAN solution to an enduring plastic decontamination problem
Nextek’s solution, COtooCLEAN. uses super-critical CO2 as a solvent to remove contaminants meaning recycled plastic films can be used in food packaging. The process has a 60% lower carbon footprint than virgin plastic production and current disposal practices.
Recycling food-grade plastic film has long been one of the packaging industry’s greatest challenges. When Professor Edward Kosior was told it was impossible, he did not see a dead end but an opportunity — transforming post-consumer polyolefin film back into high-quality, food-grade resins.
Kosior, who is the Managing Director of recycling solutions provider Nextek, assembled a team of scientists for this task. “My focus has always been on developing low-carbon solutions for the world’s most pressing recycling challenges,” said Kosior. “The gauntlet had been thrown down, and we were determined to rise to the occasion.”
A major step towards true circularity
Solving this intractable problem is key to creating a truly circular system for all types of flexible packaging, which we rely on to protect and extend the shelf-life of packaged meats, ready meals and other food products. The key to closing the loop on this valuable resource is to ensure it can be decontaminated and recycled into a resin that meets strict food safety requirements.
Boosting circularity for these types of soft plastics has the potential for massive impact. In 2021, consumers in the UK and EU used more than 2.8 million tons of polyolefin films – such as LDPE, LLDPE HDPE and PP – in consumer packaging, including direct food contact materials.
However, according to global environmental NGO WRAP UK, only 6% of these plastics are recycled due to the decontamination problem. This is mainly because there is currently no effective way to clean post-consumer flexible plastics. Some chemical methods, such as solvolysis, are being explored, but they are typically energy-intensive and require significant capital investment.
Introducing the COtooClean procedure
Kosior and his team are taking a different approach. Their key insight was that CO2 could be used to remove contaminants from the plastic films. The CO2 can be sourced from fermentation processes such as breweries, where it is a natural bi-product, or other industrial processes.
Drawing from other applications, they knew that when CO2 is converted into a super-critical fluid, it takes on unique properties, entering an unusual state that combines both liquid and gas-like characteristics.
These super-critical fluids have a density similar to a liquid but a viscosity closer to a gas: properties that make them excellent solvents.
While the use of supercritical CO2 as a solvent is known, the cleaning of soft plastics prior to recycling is entirely new. This is the first time this technology will be brought to a commercial scale. Kosior and his team have named the process COTooClean. “We're extracting organic contaminants from films that could otherwise migrate into foods,” said Kosior.
Significant carbon footprint reduction
The COtooCLEAN process delivers significant environmental benefits. A detailed Life Cycle Assessment has established savings of approximately 3.4 tons of CO2 per ton of polyethylene produced compared to virgin plastic production and current disposal methods. That’s a 60% reduction in carbon footprint.
At the other end of the process, there is very little waste to deal with as any extractants are separated and the carbon dioxide is recycled. The super-critical CO2 itself turns into a gas and is converted back into a super-critical fluid, which is reused as a solvent.
Initial lab results using super-critical CO2 in this way were promising, further validating Kosior’s insights. Encouraged by the findings, the team launched an extensive research programme.
Bringing COtooClean from lab to reality
After several years of lab work to refine the technology, Kosior’s company Nextek was ready to demonstrate it at production scale. That’s where the Alliance to End Plastic Waste’s provided support. In December 2022, Nextek won the Alliance Prize in Circular Solutions for Flexibles. The funding from the prize is being used to establish a demonstration plant to assess whether the solution is practical and commercially viable at scale. This is crucial for the approach to have a significant impact on plastic recycling rates.
“The Alliance funding has been vital to accelerating this innovation from R&D into commercial practice,” said Kosior.
Coveris as scale-up partner
Since then, Nextek has been working to assemble strategically aligned partners for the venture. It recently announced its partnership with sustainable flexible packaging provider Coveris, which will operate the demonstration plant. There has been a meticulous process of due diligence and planning for the demonstration plant involving detailed business analysis, contracts and legal agreements. This has provided a strong technical and commercial basis for the demonstration and building of a full-scale plant.
Work is underway to build the demonstration facility at Coveris’ ReCover Louth site in Lincolnshire, a county in the East of England. Construction is expected to take 9 months, with a further two months for commissioning the plant.
During a two-year demonstration phase, the aim is to test different feedstocks including household waste, post-industrial waste and supermarket back-of-store packaging, while simultaneously gathering key data, such as carbon footprint reduction impact, decontamination performance and feedstock variability needed for regulators.
Kosior said that would mean that the upscaling in a commercial plant has the potential to have a huge impact on a problem that is at the core of the waste plastic challenge. “This project is the most exciting and important innovation we have ever worked on.”
Stay in the loop
Subscribe to our newsletter for the latest news and updates from the Alliance